Mid-Land Blog
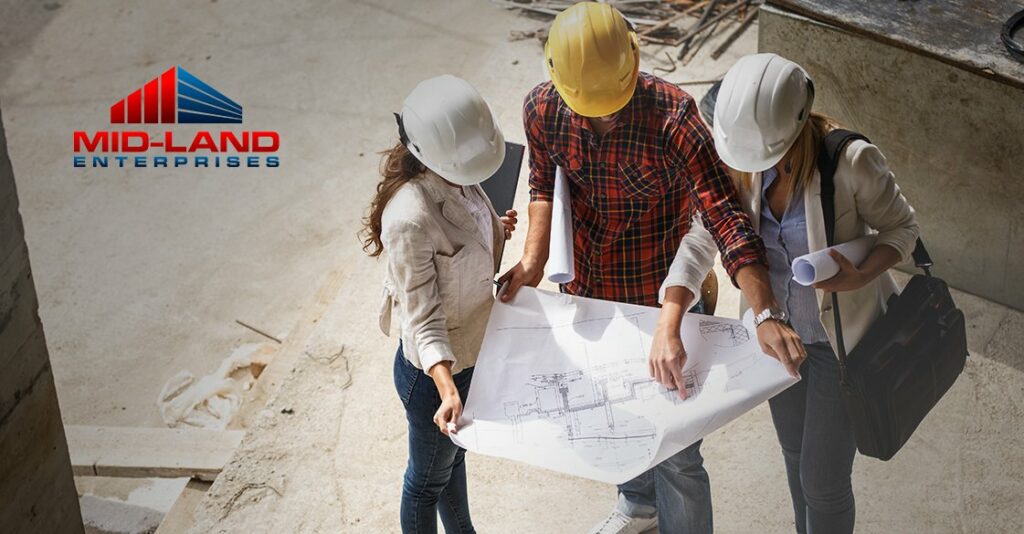
How to Organize Your Job Site Using the 5S Method
As a contractor or a project manager, you know each job varies from the next, but that doesn’t mean your methods have to. Every job site is different and will have its own set of unique conditions, but having a set organizational process in place is a great way to create a foundation for you and your team to successfully adjust to any demands that new projects may throw your way.
An organizational system that has proven to be extremely beneficial for construction projects is the 5S Organization Methodology. Sometimes referred to as the “5S Method,” this workplace housekeeping system is part of a continuous dedication to lean manufacturing.
No matter where your projects take you or how the conditions vary, using the 5S Organization Methodology can help you and your team keep standard procedures in place to help reduce waste and optimize productivity by maintaining an orderly workspace.
1. Sort
With a sorting process, unnecessary obstacles that affect production are easily eliminated and communication about team responsibilities improves. For example, sorting your tools and equipment not only saves time and space, but it also identifies annoyances in the workflow allowing them to be quickly remedied. If a tool you often use is not always easy to get to, you and your team should communicate with each other and decide on the best location for it and whose role it is to make sure it finds its way back there. Many small changes can result in a dramatically more efficient work day.
2. Set In Order
Being able to find what you need when you need it is the ultimate process for eliminating waste. The standardization of workplace order reduces time waste and leads to a leaner inventory. This means things can be found when they are critically needed. Unsafe conditions are also identified in this step since order can create a more predictable workflow leading to less risk.
3. Shine
Not only should you focus on where your tools are, but also monitor their condition. The concept of “shine” means taking pride in your work and keeping your equipment in proper working order. Keeping your tools in the right condition can help identify when to replace a tool as the defects of wear and tear become more obvious. This helps guards against workplace incidents and keeps those on the job site safe.
4. Standardize
When having multiple people work together on a project, it is important for your team to fully understand and implement standard operating procedures. Having total team “buy-in” creates an equal working relationship where everyone is expected to do their part to maintain the levels of excellence. Standardization provides consistency for your team when going from project to project, helping reduce errors, improve efficiency, and increase overall productivity.
5. Sustain
As with any great idea, execution is key. When implementing improvements, it is important to set aside time to ensure that your operations are continuing to work effectively. By clearly defining set standards and inspecting their performance, you are able to ensure that your methodology will be effective long into the future.
At Mid-Land Enterprises, we know how important it is to maximize productivity and efficiency across projects. That’s why we use the 5S Organization Methodology as part of our continuous dedication toward improvement. If you’re interested in streamlining your company’s workflow and improving operations, download our free 5S Guide to Organization today.